Identify the Carpet that Meets Your Needs
Your facility: The first step is to clearly define your facility’s requirements. Some questions to ask yourself include:
- What type of facility are you carpeting?
- Within that facility, what specific area is receiving new carpet
- How long will the carpet will be used (life cycle)?
- What types of dirt will people or machines track into the facility?
- Is the carpet part of a remodel or a new installation?
- Will installation require access to the subfloor?
- Does the space include modular furniture?
Facility location: To maximize performance, you must also determine where the carpet is going to go within the facility.
Below are some location-specific questions to ask:
- On a typical day, will people or machines spill, stains, or track dirt into the building? If so, what type of spills? Food stains? Coffee or chemical spills?
- What will the frequency of spills be? Excessive? Occasional?
- What about moisture? Do you need a moisture-permeable or impermeable backing?
- Will the flooring receive exposure to harsh chemicals, intense sunlight, or atmospheric contaminants (such as nitrous oxides or ozone)?
- Will there be lots of foot traffic? Wheelchairs? Supply carts?
The Right Carpet for Any Environment
Today’s carpet options include a wide variety of choices in style, fiber composition, and color. Whether you are specifying broadloom or tile for a corporate office, school, or public space or purchasing an area rug for a boutique hotel. New technology can produce multilevel loop and cut-loop patterns with diamond, bow, pin dot, fleur-de-lis, or other designs.
Carpet adds personality to any workplace, whether formal or bold. In hospitality settings, it can provide directional clues to move people to registration areas or elevators. In healthcare settings, carpet can be soothing and emotionally healing. It can quiet a computer lab in schools. In retail, carpet can complement merchandise displays.
For more information, download the CRI Model Specification for Commercial Carpet
To match the best carpet to the proper end-use, you should consider:
- Carpet and Rug Construction
- Dyeing and Color Selection
- Size Options
- Quality and Performance Requirements
- Insulation
- Sound Absorption
- Cushion
Understanding Carpet Construction
Carpet construction, which may be loop, cut, or combinations of the two, determines its look and performance. In corridors, lobbies, offices, classrooms, hotel rooms, patient care facilities, and other public areas, loop styles with low dense construction retain their appearance and resiliency and provide a smooth surface for rolling wheelchairs or food carts. Cut pile or cut and loop pile carpets are optimal for administration areas, libraries, individual offices, and boardrooms.
Various types of high-performance backing systems provide additional advantages including high tuft binds, added stability, imperviousness to moisture, and resistance to edge raveling. Overall, it’s important to consider the functional needs of each area when selecting your carpet type and backing.
Commercial carpet is primarily manufactured by tufting or weaving. While each process produces quality floor coverings, tufted carpet accounts for 95 percent of all carpet construction. Both tufting and woven manufacturing advanced technology to produce a myriad of carpet patterns and styles.

Tufted Carpet: Tufting is the process of creating textiles, especially carpet, on specialized multi-needle sewing machines. Several hundred needles stitch hundreds of rows of pile yarn tufts through a backing fabric called the primary backing. The needles push yarn through a primary backing fabric, where a loop holds the yarn in place to form a tuft as the needle is removed. The yarn is caught by loopers and held in place for loop-pile carpet or cut by blades for cut-pile carpet. Next, machines apply secondary backings of various types to render a variety of performance properties.
Here are some key steps in the tufting process:
- Yarn enters the tufting machine from cones on creel racks (or from big spools called beams).
- The primary backing feeds into the machine.
- Yarn and primary backing come together in the machine.
- Needles on a needlebar feed yarn through the tufting machine. Needles repeatedly penetrate or tuft into the primary backing.
- The tufted carpet is mended and inspected.
- Carpet is rolled onto large rolls for the next step (dyeing or backing).

Tufted Carpet: Tufting is the process of creating textiles, especially carpet, on specialized multi-needle sewing machines. Several hundred needles stitch hundreds of rows of pile yarn tufts through a backing fabric called the primary backing. The needles push yarn through a primary backing fabric, where a loop holds the yarn in place to form a tuft as the needle is removed. The yarn is caught by loopers and held in place for loop-pile carpet or cut by blades for cut-pile carpet. Next, machines apply secondary backings of various types to render a variety of performance properties.
Here are some key steps in the tufting process:
- Yarn enters the tufting machine from cones on creel racks (or from big spools called beams).
- The primary backing feeds into the machine.
- Yarn and primary backing come together in the machine.
- Needles on a needlebar feed yarn through the tufting machine. Needles repeatedly penetrate or tuft into the primary backing.
- The tufted carpet is mended and inspected.
- Carpet is rolled onto large rolls for the next step (dyeing or backing).
Woven Carpet: Woven carpet is created on looms by simultaneously interlacing face yarns and backing yarns into a complete product, thereby eliminating the need for a secondary backing. A small amount of latex-back coating is usually applied for bulk. Principal variations of woven carpet include velvet, Wilton, and Axminster.
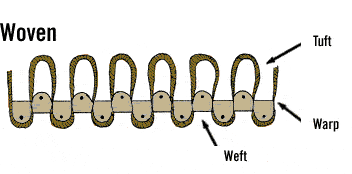
Understanding Dyeing
Dyeing is the process of coloring fiber, yarn, or carpet with dyestuff. Manufacturers can achieve coloration in carpet three times in the manufacturing process: during fiber development, before tufting the carpet, or before applying the secondary backing.
The end use of the product determines the type of dye method. For example, if a customer is concerned about color fading in a setting with large windows, the manufacturer may recommend a solution-dyed product with superior colorfastness. If the customer wants a wide variety of bright colors, the manufacturer might recommend yarn dyeing or space dyeing.
Different Dyeing Methods
Pre-dyeing of yarn includes both solution dyeing and yarn dyeing.
- Solution dyed: Synthetic yarn that is extruded and the filaments are impregnated with pigment. Known for outstanding colorfastness.
- Yarn dyed: Yarn is dyed before carpet is manufactured. Yarn dyeing includes multicolor space dyeing and solid color yarn or skein dyeing.
Post-dyeing of carpet methods include: beck dyeing, printing, and continuous dyeing.
- Beck dyeing or piece dyeing: With these methods, carpet is dyed “in a piece” using a large beck, or vat, of dyestuffs and water. This takes place after tufting, but before other finishing processes.
- Printing: Printing involves the application of colored dyestuffs using screens, rollers, or inkjets onto the face of the carpet.
- Continuous dyeing: Continuous dyeing involves the application of dyestuffs as the carpet moves in open width under the dye applicator. The process is called “continuous” because it can be used to dye an unlimited quantity of 12-foot-wide carpets, sewn end to end. (This is most often used in residential carpet.)
Using Color and Pattern
Floor coverings make a dominant fashion statement in indoor settings. Colors and patterns in a carpet can create a distinctive atmosphere, serve a practical purpose, or send a message.
Within a facility, bright colors with contrasting highlights can differentiate department or team areas. An accent color on the floor can establish a break between the floor and the wall or stairway. A printed or tufted pattern carpet can reinforce a corporate identity.
Color selection of carpet is as diverse as the imagination. Choose quiet colors such as neutral earth colors or the blues of sky and water for a soothing effect or a corporate look. Select warmer colors like reds, maize, and shades of orange to create a mood of energy and vitality. Mid-range colors and multicolor blends are best for hiding soil near entrances. Many carpet manufacturers will produce custom colors and constructions to meet your individual design specifications.
When it comes to carpet, you decide what you want it to accomplish and how you want it to look and feel in your environment.
A Size to Suit Every Purpose
Broadloom Carpet
Most commercial installations select broadloom carpet to produce fewer seams, ease installation, and obtain certain moisture benefits. Broadloom carpet can be 12 feet, 13.5 feet, or 15 feet in width. Broadloom carpet can offer large pattern repeats and the ability to pattern match. For many years, commercial installations used broadloom carpet almost exclusively.
Six-Foot Carpet
Six-foot-wide carpet remains a popular choice and is available in many designs with a variety of backing systems. This narrow carpet roll is often a benefit in high-rise buildings, where transporting a 12-foot roll is difficult or expensive. The narrow width may also provide cost savings where corridors or other narrow spaces exist. However, careful planning is needed to avoid additional seams.
Carpet Tile Construction and Installation
Accommodating Low Ceilings and Electronic Cables
Manufacturers offer low-profile carpet tile systems which use as little as 2½ inches of the vertical space – a value when the ceiling height is only eight feet. Businesses often choose modular carpet with a cushion backing for noise reduction and increased underfoot comfort. Manufacturers offer differing size configurations and depths of raised flooring to accommodate extensive wiring and for heat and air systems.
Determining Durability
It’s important to understand how all the individual elements that contribute to carpet performance work together to create an effective flooring system. For example, the construction method should be appropriate for the location and traffic requirements; the yarn size needs to correlate with the gauge; the backing systems should be appropriate for the desired performance, and the dye technique should align with the carpet’s intended use.
The most common trap is relying on only one single construction factor to determine if a product will meet your specifications. In other words, while pile yarn density is important, so is the gauge, the yarn size, and many other construction parameters. That’s why it’s so important for specifiers and end-users to explain how they want the product to perform and allow the manufacturers to make construction recommendations that meet those needs.
Carpet performance is associated, in part, with pile yarn density – the amount of pile yarn in a given volume of carpet face. For a given carpet weight, lower pile height and higher pile yarn density will yield the most performance for the money.
Density is also influenced by the number of tufts per inch when counting across a width of carpet. For example, a 1/8 gauge carpet has eight tuft rows per inch of width and a 1/10 gauge carpet has 10 rows per inch of width. Extra heavy traffic conditions require a density of 5,000 or more.
Appearance is an aesthetic choice, while texture retention is a performance issue. However, the two areas are closely related. Heavy foot traffic and soil can discolor carpet and should influence design decisions. Mid-tone colors and colors that blend with the general shade of local soil are the best to use in high-traffic areas, especially near entrances. Manufacturers often recommend “walk-off” carpet systems for entryways. Walk-off carpet is designed to clean shoes of dirt and moisture and protect entrances from excess soiling. In addition, walk-off carpet systems increase foot safety and reduce slip-and-fall accidents. Eight feet of walk-off carpet is considered optimal to protect interior carpet installations and enhance user safety and comfort.
Understanding Thermal Values (R-Values) of Carpet and Cushion
An industry-sponsored study of the thermal characteristics of carpet (R-value or thermal value) – with and without cushion – conducted by the Georgia Institute of Technology, concluded that a carpet’s ability to maintain temperature is more dependent on the total thickness of the carpet than on the type of fiber in the carpet.
When the carpet R-value is not available, the study suggested multiplying the total carpet thickness measured in inches by a factor of 2.6 to approximate the carpet’s R-value. The study also found that R-values are additive for any combination of materials. For example, a combination of carpet with an R-value of 1.3 and a prime polyurethane cushion with an R-value of 1.6 will yield an overall R-value of 2.9.
Download Understanding Thermal Values (R-Values) of Carpet and Cushion, with more detailed R-value information that was taken from the study conducted by the Georgia Institute of Technology School of Textile Engineering.
Acoustics and Commercial Carpet
Sound Absorption
Sound Transmission
Match Cushion to Carpet for Best Results
Selecting the right backing system is critical for the performance and life of your carpet. Cushion provides resilience, acoustical/thermal insulation properties, and comfort underfoot. It is especially important that you select your carpet product and backing according to the expected traffic patterns and the manufacturer’s requirements for thickness and density. Carpet tile is generally designed to function without the need for additional cushion.
There are three main types of carpet cushion used in commercial broadloom applications: fiber, rubber, and polyurethane foam.
- Fiber cushion is made of rubberized hair, rubberized jute, synthetic fibers, or recycled textile fiber.
- Rubber cushion consists of flat rubber, textured flat rubber, rippled waffle (Class I only), or reinforced rubber.
- Polyurethane foam cushion is made of grafted prime polyurethane, densified polyurethane, bonded polyurethane, or mechanically-frothed polyurethane.
The three classes of commercial carpet cushion applications are Class I, Class II, and Class III.
- Class I (moderate traffic): Typically, this class includes executive, administrative or private offices in office buildings, banks, schools, and healthcare facilities.
- Class II (heavy traffic): Generally, this class includes clerical areas, corridors, patient’s rooms, lounges, classrooms, and public areas in healthcare facilities, libraries, museums, hotels, motels, and schools.
- Class III (extra heavy traffic): This class includes cafeterias, nurses’ stations, public and ticketing areas, and lobbies in office buildings, airports, and healthcare facilities.